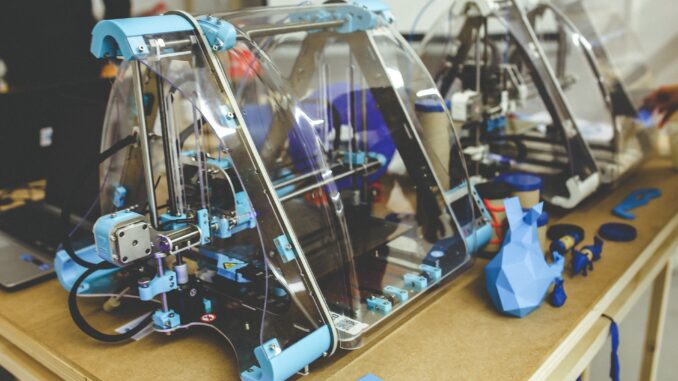
There is no doubt that Electric vehicles are one of the paths to a more sustainable, cleaner, and a safer world. 3D has the potential to make this journey easier and less expensive, as well as exponentially enhance the rise of electric vehicles.
EVs & 3D Printing
The components of an electric car differ significantly from those of an internal combustion engine (ICE) vehicle. To make the electric vehicle lighter, more energy-efficient, and vibration-free, 3D printing can be used to manufacture components. 3D printing will allow for faster manufacturing and mass customization with the press of a button.
How 3D Printing Can Disrupt The EV Sector?
Casting is one of the oldest and most expensive manufacturing processes, with the most important phase being the preparation of the sand mould. The use of digital sand moulding for preparing sand moulds to enable subassembly reduction has recently begun.
Even before metal casts can directly make massive metal parts, 3D printing-enabled custom casts can bring about tremendous advancement.
The advancement of sand 3D printing technologies to improve the capabilities of the old casting industry may become more widespread as it can handle high throughput manufacturing as required by the automobile industry.
Before beginning mass production of any model, car manufacturers typically conduct process verification. The process is verified to ensure that all of the individual components are made and assembled correctly according to design.
Advantages Of 3D Printing In EV
Highly detailed, accurate to micro levels, and smooth scale models made using 3D printing technology are frequently used to exhibit design concepts. These models are also useful when CAD models are insufficient for identifying design flaws.
#1 Personalization
3D printing allows you to build a wide variety of designs that may be further customised to your client’s needs with anything from a minor texture on your dashboard to a completely personalised exterior.
#2 Rapid prototyping
It is the foundation of research and development (R&D), and 3D printing has supplied that foundation to the electric car sector. With the ability to make modifications with the press of a button, new and innovative ideas and designs may be immediately tested.
#3 Lower Capital Investment
3D printing technology is more cost-efficient and requires less infrastructure than traditional manufacturing set-up costs over a longer period.
#4 Lower Operational Expenditure
3D printing will enable us to replace modern-day physical inventory with digital libraries. The components can be produced as needed. As a result, assembly times will be reduced, and the prospect of Just-in-time manufacturing will increase.
Now that we have discussed the general advantages of 3D Printing let us look a bit deeper.
Impact Of 3D Printing in the Life Cycle Of EVs
Design Stage
#1 Lightweight Body Parts
Unlike traditional ICE vehicles, electric vehicles are powered by batteries. The vehicle’s range (the maximum distance that can be travelled once the battery is fully charged) is directly proportional to its weight.
Thus,
- The weight should be as light as possible to achieve the greatest possible range for a given energy reserve.
- It is an issue because maintaining the strength of the part is also important.
- Just decreasing the part thickness to reduce weight will also reduce strength.
- As a result, the geometry and topology must be optimised in relation to the loads operating on the component.
This means that the part must go through design and validation cycles and 3D Printing can be of great use at this stage.
#2 Configuration of the Chassis
Electric vehicles are propelled by electric motors rather than engines. As a result, the transmission and battery pack must be located and optimised to take up as little space as possible to keep the car light. As a result, chassis configurations must be determined using small-scale prototypes.
3D printing techniques such as FDM can be utilised to quickly manufacture scale models and evaluate the options.
#3 Enclosures for Fire and Safety
Batteries must be protected from heat and fire, and because batteries generate heat during the discharge cycle, the enclosure must appropriately dissipate that heat. As a result, well-ventilated enclosures with vent holes must be created.
Such intricate designs are simple to create using 3D printing. For 3D printing, flame-resistant and flame-retardant materials such as ULTEM 9085 are available.
Production Stage
#1 Metal part tooling
Metal casting/forging/machining is commonly used to make parts such as steering knuckles, suspension mounting brackets, and electric motor housings. They are then CNC machined using specialist tools for surface polish and fastening hole drilling.
To reduce the number of tool-passes and operations required to obtain the geometry, specialized cutting tools are required. For example, centre drilling and chamfering can be done with a specific tool that does both at the same time.
Metal 3D printing can be used to create such specific tool bases, which can then be fitted with carbide or cubic boron nitride cutting tool inserts.
#2 Sheet Metal Parts Tooling
Stamping die tools would be required for the mass manufacture of sheet metal items. Traditionally, the geometry of stamping dies is machined on 5-axis machining centres to produce metal dies that can withstand thousands of cycles.
However, for experimental and form validation reasons, FDM 3D printed tools made of ULTEM 9085 that have shown to endure pressures up to 70 MPa and can last 300 pressing cycles can be utilised.
#3 Die Casting Tooling
Metal dies with complex geometries and cooling channels would be required for pressure die-casting metal items. Inserts are used to create such complicated geometries.
Companies have recently begun to investigate ways to 3D print dies to provide conformal cooling channels that cut cooling cycle times.
#4 Plastic Parts Tooling
Dashboards, instrument panel covers, brake handles, and other injection moulded interior pieces of automobiles are composed of plastic. The design, development, and manufacture of complicated injection mould tooling takes several months and costs money.
As a result, companies are looking into techniques to create 3D-printed injection moulds that require minimal machining. This also saves a lot of money on design and development.
#5 Fixtures and Jigs
Assembling multiple components necessitates the use of unique work-holding aids that smooth out the operation and save assembly time. Jigs and fittings protect workers and reduce hand motions to improve accuracy.
3D printing is an excellent way to create jigs and fixtures at a low cost. In addition to physical handling, various robots that handle parts in the factory would require grippers that perform a certain set of tasks. When a new vehicle model is introduced, all following manufacturing line handling must be modified.
The robotic grippers may be 3D printed, which saves time and money. There are several ESD materials available for 3D printing that prevent static electricity buildup on their surface, preventing electrical component damage during assembly.
The Aftermarket Stage
The OEM supplier industry frequently survives on orders from other vehicle companies. It is likely that at some point, production of a given part will be halted.
Companies intend to disrupt the ecosystem by investing in 3D printing companies that can make spare parts for them to provide seamless aftermarket services.
Although 3D printing is a sluggish process that cannot match mass production numbers, businesses will gain in the future from the flexibility, reduced costs, and faster delivery times afforded by 3D printing methods.
The cost of investing in 3d printer machines saves inventory and stock holding costs with digital printing and smart inventory models.
Conclusion
While 3D printing is being used to aid in the processes of design, development, and manufacturing of automobiles, including electric vehicles, direct 3D printing of vehicle parts is not yet capable of meeting full-scale production demands, and thus remains feasible only for limited-scale production runs.
However, in the early stages, when market adoption and customer acquisition are critical, additive manufacturing and 3D printing are excellent solutions to get models on the road.
Although the exact break-even point between mass production and 3D printed parts is not yet clear, global auto giants such as BMW and Volkswagen have demonstrated that additive manufacturing can be used to produce up to 100,000 parts per year, which is still a reasonable number given the current levels of EV adoption in India.
3D printer firms such as Stratasys, 3D Systems, EOS, and HP among others, are directly striving to improve the technologies even further to enhance build volumes and speed to satisfy the demands of mass production and to directly contribute to the mainstreaming of 3D printing.