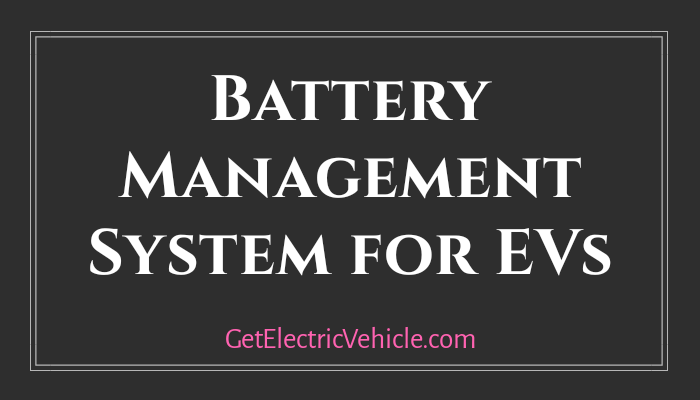
A battery management system is an electronic system that manages a rechargeable battery.
A Battery management system is the brain of a battery pack
A battery pack with a built-in battery management system is a smart battery pack. A smart battery charger that can be connected to the smart battery’s BMS through CAN bus or any other communication protocols charges the battery. It’s necessary to use a smart battery charger to charge a smart battery.
Why BMS in Electric Vehicles?
Li-ion battery, one of the common batteries that use in an electric vehicle are costly and prone to damages. The life span of the battery is important!!
- Electric car battery life expectancy: How long EV battery lasts?
- Electric car motor life expectancy: How long EV motor lasts?
- Electric vehicle life expectancy: How long an EV lasts?
The chances of thermal runaway of Li-Ion battery are much higher and each cell has to be individually monitored to prevent the damage.
The mobile applications would be efficient (the battery lasts long) only if the battery operates at maximum efficiency. With proper thermal and power management, a battery shall be operated optimally to get the maximum out of it.
Functions of the Battery Management System
The primary function of a BMS is to protect the battery from damages in a wide range of operating conditions.
The operation of a battery outside the safe operation area is prevented
- Internal switches to isolate battery when it tends to operate outside of the safe operating area.
- Requesting the devices to reduce the power demand from battery
- Actively controlling the environment by heaters, coolers, and fans
Other functions of BMS are
- Energy Management
- Cell balancing
- Controlling its environment
- Etc. etc.
A brief explanation of the functions of a Battery Management system
A battery management system does have the following functions.
It monitors Voltage, Current, Temperature, State of Charge (SOC), State of Health (SOH), Depth of Discharge (DOD), State of Power (SOP), and coolant flow.
Using the above parameters, a BMS calculates a few values that are useful and helps out to protect the battery.
The following are a few of them.
Maximum charge current, Maximum discharge current, Energy delivered since the last charge, Internal impedance of a cell, Charge stored in the battery, Total energy delivered since first use, Total operation time since first use, Total number of cycles.
A battery management system communicates with the low-level hardware through sensors and with human-machine interfaces (HMI) using CAN bus. Instrumental cluster in an electric vehicle (any vehicle) indicates the user information from the battery management system.
The most important function of BMS are listed below
- Over-current protection
- Overvoltage protection
- Under-voltage protection
- Over-temperature protection
- Under temperature protection
- Overpressure protection
- Leakage current detection
A BMS acts as an intermediate device that connects the load from battery to prevent excessive load changes to protect the battery.
Cell balancing to improve the performance of the battery is another function of BMS. All the cells in a battery are being kept at an equal state of charge dissipating excess charge in some cells, regulated charging to the cells, and shutting off some shells.
Components of a Battery Management System (BMS)
A battery management system is an electronic control circuit that monitors battery. Many BMS ICs are available in the market. Eg. Texas Instruments have the BMS IC TPS65011
What are the components of a battery management system?

Current sensor
The total current and currents in individual cells of the battery are sensed to calculate the total energy that stored and utilized form the battery.
The current consumption over time would give you the energy remains in the battery.
Voltage sensor
Cell voltage and battery voltage monitoring are the functions of a battery management system in an electric vehicle. Voltage sensors connected to the battery monitor open-circuit voltage and the potential difference when the battery is loaded.
The health of the battery highly depends on the cell voltage. The voltage range where the battery is allowed to charge and discharge should be strictly followed for the best performance from the battery. For example, a lithium-ion battery of nominal voltage 3.6V has maximum and minimum voltage ratings of 2.8V and 4.2V respectively [Reference].
One method used to check if the battery fully charged measuring open-circuit voltage. Thus the charging of the battery can be regulated.
Static switches and controllers
Each cell packed in an electric vehicle battery is individually monitored using a battery management system. The static switch such as FET and the controller together connects and disconnects cells from the load and charging circuit if necessary.
Temperature sensor
A Li-ion battery, which is the common battery technology in a modern electric vehicle is sensitive to temperature. A short circuit results in consecutive heat generation and thermal runaway of the battery.
Thermal management is highly important in a battery. Temperature affects the efficiency of the battery as well.
Active cooling might be triggered by measuring the temperature of cells in a battery pack to protect them from fire.
Battery State Estimation algorithm
Two important parameters of battery are the State of Charge and the State of Health. SOC indicates the charge level in a battery (%).
There are two types of SOCs
- Absolute State of Charge (ASOC) – when the battery in new
- Relative State of Charge (RSOC) – available charge taking capacity fade into account
Generally, SOC refers to RSOC.
The state of health indicates the ability of a battery to perform as if it’s new. The ratio of current energy capacity to the capacity of the battery when it was new is defined as SOH.
Computation of State of Charge (SOC) uses different algorithms such as
- Coulomb counting method
- Open circuit voltage method
- Impedance measurement method
- Artificial neural network fuzzy logic
- State space model with Kalman filter
The state of health estimation includes the number of charge-discharge cycle calculations.
User interface
The user interface indicates the status of the battery and other relevant data to the user. Any inputs from the user would also be sent to the battery management control unit if necessary from the user interface.
Mathematical model of battery
A battery model is necessary to check the working of a battery management system. The model developed using mathematical equations can be used for analyzing a BMS.
You can read: How to develop a battery model for electric vehicle simulation?
Real Time Clock
To time stamp the measured data, estimation of life, energy estimation, etc. require time signal. A real-time clock in BMS helps out here.
Memory
The data collected and processed will be stored for further analysis. Life estimation, state of health estimation, etc. requires the initial data stored in memory.
Factors to be considered while designing a BMS
The desirable properties of a battery management systems are listed below
- Power consumption of BMS should be as minimum as possible
- Idle power consumption should be minimum
- The BMS shall be run using the energy from the battery that it monitors
Conclusion
A Battery management System for an electric and hybrid electric vehicle is necessary to protect and manage high voltage battery. Li-ion battery that used in electric vehicle damages easily if it is not well maintained.
Uncontrolled charging, discharging, high temperature, etc. damage the cells. A battery management system helps out to protect the battery from these damages.
Don’t forget to share the post with your friends and follow us on Facebook, LinkedIn, Twitter, Instagram, and YouTube!
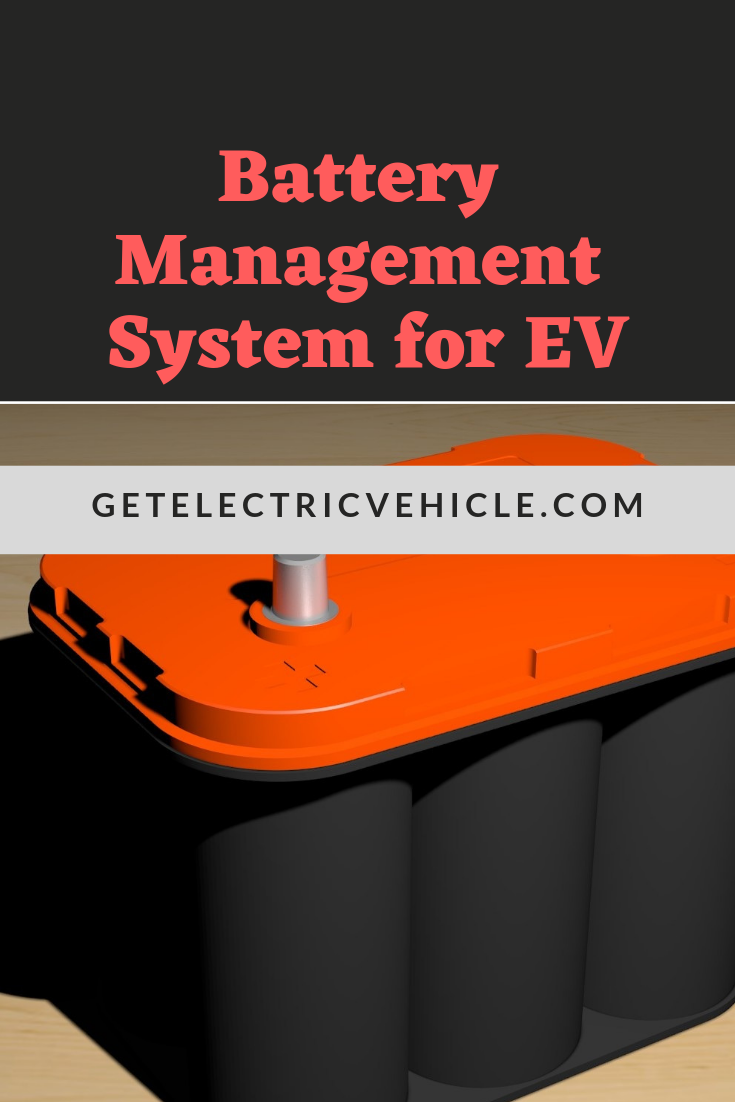
Key points
- BMS is essential in an electric vehicle battery system
- Protection, energy management, cell balancing etc. are the functions of a battery management system