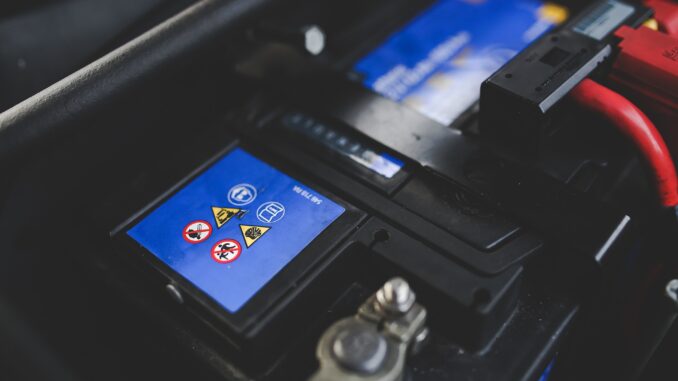
By 2050, it is expected that 74% of Europe’s cars on the road will be battery-powered. Despite the rapid adoption of electric vehicles, there has been little discussion about standardizing battery types.
The internal combustion engine will be gradually supplanted by the growth of the battery-powered electric car over the next half-century. The current generation of these cars is powered by lithium-ion (Li-ion) batteries, which are expected to dominate this market for the foreseeable future. The question of whether governments should mandate increased battery standards is not new. However, it is more difficult than before.
So let us weigh some facts on the battery standardization movement.
Standardization: Being Nice To the Environment
Green is the most compelling argument in support of increased standardization. Although electrification in road transportation is promoted as a way to reduce emissions, disposing of all these used batteries presents new environmental issues.
According to a recent analysis, the number of electric vehicles sold in 2017 will generate 250,000 metric tonnes of battery waste. This estimate excludes other electric vehicles, such as electric buses.
The hazardous business of managing this garbage is made more difficult by the fact that different manufacturers employ different battery chemistries and their packs come in a variety of forms and sizes.
How standardization helps the environment
- Standardization helps the environment.
- The removal of the packs would be less expensive and less dangerous if there was less variety in size and shape.
- It may also pave the door for greater automation in the waste disposal process.
- At the very least, tighter rules around the labeling of batteries would be of use.
- All this would make it easier to recycle or utilize the batteries.
Standardization: Way To Save Millions
The environmental argument feeds into a cost-benefit analysis. First and foremost, mass production of Li-ion batteries will reduce costs for vehicle OEMs. Furthermore, vehicle manufacturers are frequently both legally and financially obligated to remove and recycle these batteries. These costs will also be reduced as a result of standardization.
Secondly, in the next few years, second-life uses for these batteries will emerge as a lucrative sector. OEMs are expected to profit $67 on average for each battery unit that is repurposed rather than recycled. Standardization makes the repurposing process safer and easier, which can benefit both manufacturers and consumers financially.
Now let us look at EV battery standardization in the Indian context.
Standardization: India’s Position
In India, Niti Ayog’s electric vehicle mobility plans encourage the sale of only electric vehicles after 2030 to reduce carbon emissions and broaden the reach of clean energy. Currently, the energy source for the motor or prime mover in this generation of EVs is Lithium-ion (Li-ion) batteries. Because of its temperature tolerance, wide usability, long life, and high energy density, this battery type is projected to dominate markets for a long time.
Despite the growing popularity of electric vehicles, batteries are still non-standardized to maintain the uniqueness of EVs in terms of sales and competitiveness among manufacturers. However, standardization offers its own set of advantages in terms of creativity, knowledge retention, flexibility, and the requirement for compliance.
Currently, in the Indian EV market, 2-wheeler sales are growing faster than 4-wheeler sales and will continue to expand rapidly, making it the leading challenger in battery use. According to the FADA, e-two-wheelers would account for 3.6% of total 2-wheeler sales in India in 2022. (Federation of Automobile Dealers Association of India). According to Statista, this penetration will rise to 47% by 2030 if current trends continue.
However, manufacturers use a variety of battery chemistry, forms, and sizes to create packs that meet their specifications, creating a tricky scenario for sustainability or reuse. As a result, standardization is a solution to all of the industry’s and end users’ problems.
Standardization: Makes Battery Swapping Easier
Niti Ayog has created the Battery Swapping Policy, which includes technical features of standardization that will allow for interoperability across the battery swapping ecosystem. The standardization of batteries would make this process easier because every EV has the same battery, making it dependable to exchange regardless of whatever company built the battery. It is efficient for corporations to minimize manufacturing costs and will forge a way to use the battery in a reusable market. Currently, the load on OEMs responsible for extracting and recycling batteries will be reduced as commercial participants in safe battery disposal step forward. As markets develop, so will the use of these batteries in their second life.
Standardization: Assist With EV Charging Infrastructure
Indian car drivers are currently accustomed to refueling their automobiles using combustible fuels, which require less time and are more easily available. EVs have the same attractiveness; nevertheless, charging is time-consuming, and charging facilities are restricted in comparison to the rising sales of EVs. Battery standardization will benefit the EV infrastructure since connectors may be designed with a uniform usage strategy, lowering costs, waiting time, and design trouble. The battery may also be replaced in a matter of minutes, giving the end user confidence. Furthermore, the charging price will be standardized, with only a market-based fair value.
Standardization: Ensures Safety
Safety is a big concern in countries like India. In India, there were a few incidents where EVs caught fire and some manufacturers had to recall certain models from the market.
The Bureau of Indian standards (BIS) has issued performance standards for electric vehicle batteries to protect customer safety. According to a top consumer affairs ministry official, the national standards-setting agency that reports to the consumer affairs ministry has produced “performance specifications for electric vehicle batteries.”
The standard “IS 17855: 2022” was developed for lithium-ion traction battery packs and systems of electrically propelled road vehicles and is compatible with ISO 12405-4: 2018, according to the official.
The new EV battery standard, according to the officials, comprises the test technique for the essential characteristics of performance, dependability, and electrical functioning for the battery packs and system for either high power or high energy application.
This standard was developed with real-life scenarios for an electric vehicle in mind, such as the vehicle in parking (the battery is not used for an extended period), the battery system being shipped (stored), the battery operating at low and high temperatures, and so on. As a result, various tests are included in this standard.
Concerning the safety of batteries for electric cars, the BIS is in the process of publishing two further standards on batteries for various passenger and goods-carrying vehicles (L, M, and N categories).
The Troubles That Accompany The Standardization
Despite the benefits listed above, too much standardization across the whole EV industry is both unfeasible and undesirable. Those that create and produce the vehicles and batteries are very protective of their intellectual property. Tesla, for example, is unlikely to rapidly divulge the secrets of its latest battery chemistries.
In any case, excessive standardization would impede creativity. This is not yet a mature technology, and competition is driving innovation. The location of batteries in electric buses, for example, is a completely separate topic, but it does illustrate the ability to defy conventions in electric vehicle design. Yes, strict safety and environmental regulations are required, but we also want to encourage as much design flexibility as feasible.
Conclusion
Standardization is one part of the equation for achieving universal vehicle electrification by the mid-century mark. This will allow us to use this technology in a more environmentally friendly and cost-effective manner. The role of design flexibility and creativity will be the other half of the story. If the forecasts for 2050 are correct, the industry will need to meet halfway to provide enough flexibility and innovation to keep vehicles competitive, as well as the appropriate level of standardization to make costs manageable.