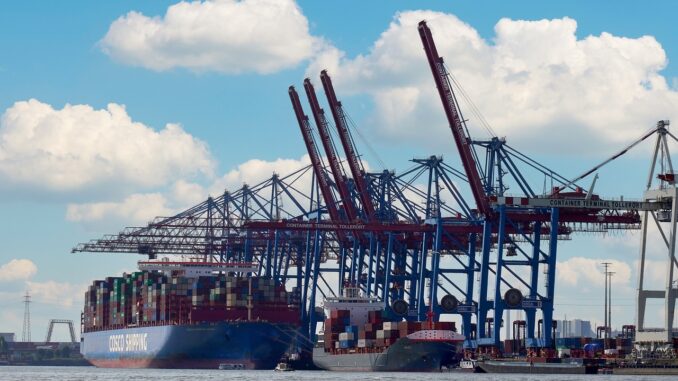
Picture this: You’re cruising down the road in your sleek, futuristic electric vehicle (EV), enjoying the whisper-quiet ride and emission-free journey. But have you ever wondered about the behind-the-scenes challenges that make this incredible transportation revolution possible?
The electric vehicle industry is not just about cutting-edge technology and zero-emission vehicles. It also involves an intricate web of suppliers, manufacturers, and logistics providers. The supply chain in the EV industry is a complex ecosystem that spans multiple continents, involving various components, raw materials, and intricate processes.
In this article, we will explore the depths of the EV supply chain, from global suppliers to raw materials, manufacturing complexities to logistics and distribution, and the exciting world of supply chain risk management.
Electric Vehicle Supply Chain
#1. Global Component Suppliers
The production of electric vehicles relies on a vast network of global component suppliers. These suppliers provide essential parts such as batteries, electric motors, power electronics, and charging infrastructure coordinating these metrics is a complex and tedious job.
Also, as an EV manufacturer, relying on a single supplier for critical components or raw materials can create vulnerabilities in the supply chain.
The EV industry aims to diversify its supplier base to minimise the risk of disruptions caused by factors such as supplier bankruptcy, natural disasters, or geopolitical issues.
Identifying alternative suppliers and establishing relationships with multiple sources can enhance supply chain resilience.
Here are some major global suppliers in the EV industry.
LG Chem
LG Chem, based in South Korea, is one of the world’s largest manufacturers of lithium-ion batteries. They supply batteries to several prominent electric vehicle manufacturers globally.
LG Chem’s batteries are known for their high energy density, reliability, and safety features.
Panasonic
Panasonic, a Japanese company, is a leading supplier of automotive batteries for electric vehicles. They have partnered with Tesla to produce lithium-ion batteries for Tesla’s electric cars.
Panasonic batteries are renowned for their energy storage capacity and long cycle life.
CATL
CATL (Contemporary Amperex Technology Co. Limited), headquartered in China, is one of the world’s largest manufacturers of lithium-ion batteries for electric vehicles.
They supply batteries to various automakers, including Volkswagen, BMW, and Tesla. CATL is known for its innovative battery technologies and has been actively expanding its production capacity.
Samsung SDI
Samsung SDI, a subsidiary of Samsung Group, is a major supplier of lithium-ion batteries for electric vehicles. Based in South Korea, Samsung SDI provides batteries for various EV manufacturers worldwide.
They offer high-energy-density battery solutions and are committed to developing sustainable battery technologies.
BYD
BYD (Build Your Dreams), based in China, is a leading manufacturer of electric vehicles and batteries. They produce a range of electric cars, buses, and trucks, along with their own battery technology.
BYD is known for its vertically integrated supply chain, encompassing battery production, electric vehicle manufacturing, and charging infrastructure.
ABB
ABB, a Swiss-Swedish multinational corporation, is a significant player in the EV charging infrastructure market. They offer a wide range of charging solutions, including fast chargers, ultra-fast chargers, and charging network management systems.
ABB’s charging infrastructure enables efficient and convenient charging for electric vehicle owners.
Siemens
Siemens, a German conglomerate, is involved in the production of electric vehicle charging infrastructure and related technologies. They provide charging stations, charging management software, and grid integration solutions.
Siemens’ expertise in power electronics and energy management contributes to the development of sustainable charging solutions.
Bosch
Bosch, a multinational engineering and technology company based in Germany, is a leading supplier of various components for electric vehicles. They offer electric motors, power electronics, sensors, and charging solutions.
Bosch’s diverse range of products supports the electrification of vehicles across different segments.
These are just a few examples of the many global suppliers involved in the EV industry. The dynamic nature of the market continues to drive innovation and collaboration among suppliers, ultimately advancing the growth and sustainability of electric mobility.
Now let us look into the intricacies of obtaining the raw materials for EV production.
#2. Raw Materials and Mining Challenges
Electric vehicle batteries require a range of raw materials, including lithium, cobalt, nickel, and rare earth elements. We will uncover the complexities associated with sourcing these materials, highlighting the environmental and social challenges, such as mining practices, labour conditions, and ethical sourcing concerns.
Exploring initiatives to promote responsible sourcing and sustainable mining practices will shed light on the industry’s efforts to minimize environmental and social impacts.
Here is a list of major raw materials involved in EV production and the issues faced from a supply chain perspective.
Lithium
Lithium is a key component in lithium-ion batteries, which power most electric vehicles on the market today. The majority of lithium reserves are found in countries like Australia, Chile, and Argentina. However, mining lithium raises environmental concerns such as water scarcity and pollution.
Additionally, the increasing demand for lithium raises questions about responsible extraction practices and the long-term availability of this resource.
Cobalt
Cobalt is another essential element in electric vehicle batteries. The majority of cobalt production occurs in the Democratic Republic of Congo (DRC), where ethical and environmental issues have been raised.
Concerns include child labour, unsafe working conditions, and environmental degradation. The industry has been actively working to address these challenges by promoting responsible sourcing and investing in supply chain transparency.
Nickel
Nickel is a critical component in EV batteries, particularly for long-range electric vehicles. The growing demand for nickel raises concerns about the environmental impact of mining and processing.
Extracting nickel can have significant energy and water requirements, leading to potential environmental degradation. Sustainable nickel mining practices and efforts to minimize environmental impacts are being explored.
Rare Earth Elements
Rare earth elements (REEs) are used in the production of magnets for electric motors. These elements include neodymium, praseodymium, and dysprosium.
China dominates the production of REEs, which raises concerns about supply chain dependency and market manipulation.
Diversification of REE sources and exploration of alternatives are being pursued to reduce reliance on a single country.
Ethical and Environmental Concerns
The mining of raw materials for EV batteries raises ethical and environmental concerns. These include the displacement of indigenous communities, land degradation, deforestation, water pollution, and carbon emissions associated with mining operations.
Responsible sourcing initiatives, such as the Responsible Minerals Initiative (RMI) and the Global Battery Alliance, aim to address these concerns by promoting sustainable practices, ethical sourcing, and transparency in the supply chain.
Recycling and Circular Economy
To mitigate the environmental impact of raw material extraction, the industry is exploring recycling and the circular economy approach. Recycling EV batteries allows for the recovery of valuable materials such as lithium, cobalt, and nickel, reducing the need for new mining.
Establishing efficient recycling infrastructure and processes is crucial to minimize waste and maximize resource utilization.
As we know, making an EV is not quite the same as making an ICE-powered car. Now let us briefly look at the unique challenges faced by companies while mass-producing EVs.
#3. Manufacturing Processes and Assembly
Automobile manufacturing involves numerous stages, including stamping, welding, painting, and final assembly.
But the EV manufacturing industry has a unique set of challenges associated with manufacturing, such as the need for specialized equipment and facilities, retooling existing factories, and training a skilled workforce.
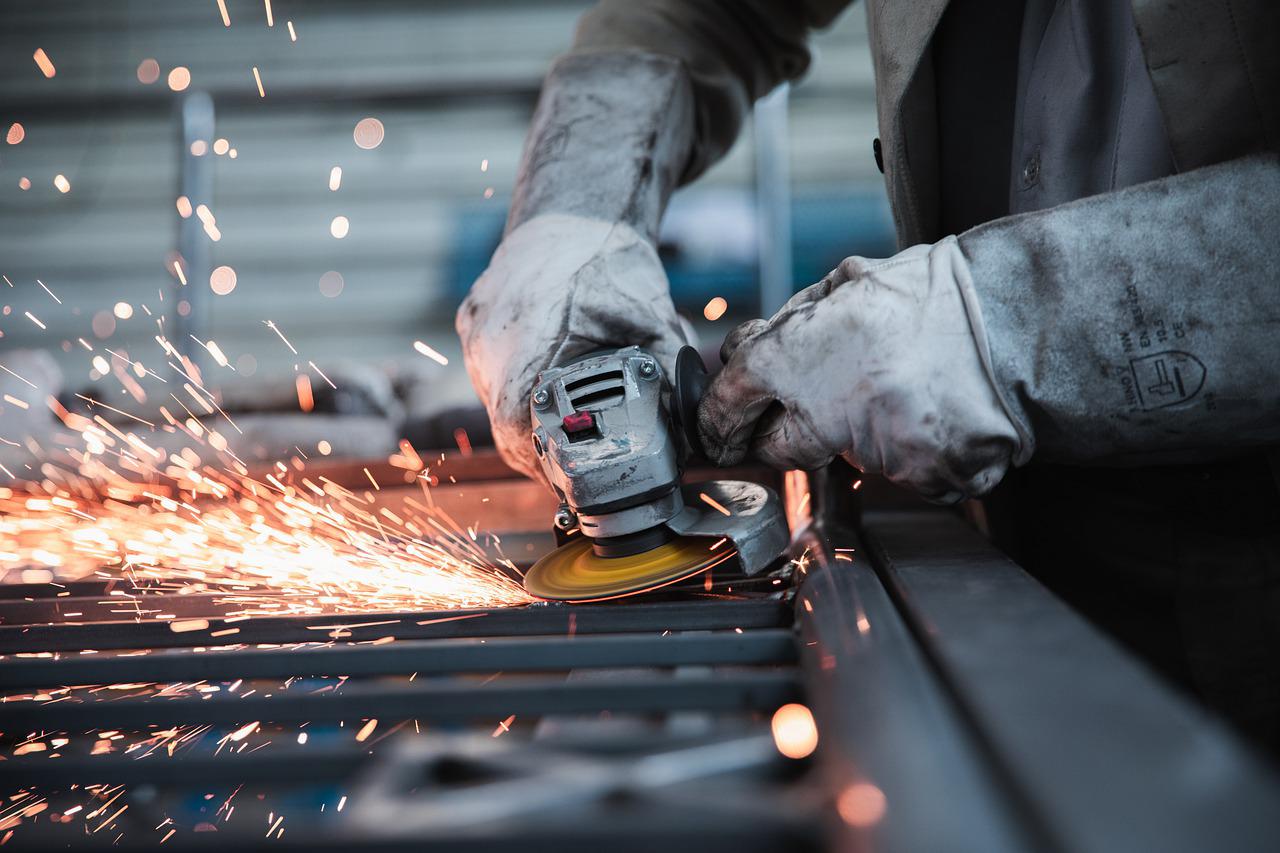
Manufacturing Facilities
EV manufacturing often requires significant changes to existing manufacturing facilities or the construction of new ones.
The assembly line needs to be reconfigured to accommodate the installation of batteries, electric motors, and associated components.
This may involve retrofitting or building new production lines, retraining employees, and adapting processes to handle the unique characteristics of EV components.
Workforce Training
As the EV industry continues to grow, manufacturers face the challenge of training their workforce to handle new technologies and processes.
Skilled technicians and engineers are needed to understand and work with high-voltage systems, battery management systems, and electric drivetrains. Training programs and continuous skill development are crucial to maintaining a competent and adaptable workforce.
The complexity of Software Integration
Electric vehicles rely heavily on sophisticated software systems to manage battery charging, energy efficiency, regenerative braking, and vehicle connectivity.
Integrating these software components into the overall vehicle system requires expertise in software development, cybersecurity, and vehicle diagnostics. Ensuring seamless integration and effective functionality can be a challenge during the manufacturing process.
Cost and Scale
At present, the production of EVs is generally more expensive compared to ICE vehicles due to the higher costs of battery technology and limited economies of scale.
EV manufacturers face the challenge of reducing costs through technological advancements, supply chain optimization, and volume production. Achieving cost parity with ICE vehicles is a key goal for the industry.
Now moving on to the logistics and distribution of EVs
#4. Logistics and Distribution
Shipping electric vehicles and their components across continents require efficient logistics and distribution networks.
We will examine the transportation challenges, including ensuring safe and secure delivery, minimizing carbon emissions in logistics operations, and optimizing the supply chain for just-in-time manufacturing.
Supply Chain Management
The EV supply chain involves multiple components and raw materials sourced from various locations worldwide. Managing the supply chain effectively to ensure the timely availability of components and raw materials for production is critical.
Ensuring supply chain transparency, optimizing inventory management, and mitigating potential disruptions, such as trade policies, geopolitical tensions, or raw material shortages, are challenges that require robust logistics strategies.
Vehicle Transport and Delivery
Transporting EVs from manufacturing facilities to dealerships or customers presents specific challenges due to their unique characteristics.
EVs often require specialized transportation equipment and handling procedures to ensure their safety, especially concerning the transportation of lithium-ion batteries.
Coordinating the logistics of vehicle delivery, optimizing transportation routes, and addressing any regulatory or permitting requirements are critical for efficient and timely delivery.
Battery Recycling and Disposal
The proper recycling and disposal of EV batteries pose logistical challenges. Establishing effective battery collection, recycling, and disposal processes that comply with environmental regulations is crucial.
Coordinating battery collection networks, logistics for transporting batteries to recycling facilities, and ensuring responsible disposal practices are ongoing challenges that require collaboration between EV manufacturers, recycling companies, and regulatory bodies.
International Trade and Regulatory Compliance
The EV industry operates in a global market, which means navigating complex international trade regulations, customs procedures, and compliance standards.
Ensuring compliance with various safety, environmental, and transportation regulations across different countries can be challenging.
Manufacturers must stay updated on changing regulations, adapt their logistics processes accordingly, and ensure smooth cross-border movements of EVs and related components.
Conclusion
As we wrap up our thrilling journey through the electric vehicle supply chain, it’s clear that there’s much more to this industry than meets the eye.
The complex supply chain in the electric vehicle industry is a crucial element in the successful transition to sustainable transportation.
Supply chain resilience and risk management are critical for the electric vehicle industry’s success. By diversifying suppliers, mapping dependencies, enhancing transparency, fostering collaboration, leveraging digital technologies, and developing robust business continuity plans, companies can strengthen their supply chains and mitigate potential disruptions.
Proactive risk management strategies and a focus on supply chain resilience contribute to the growth and sustainability of the EV industry, ensuring a reliable and efficient supply chain for electric mobility.
You May Also Like